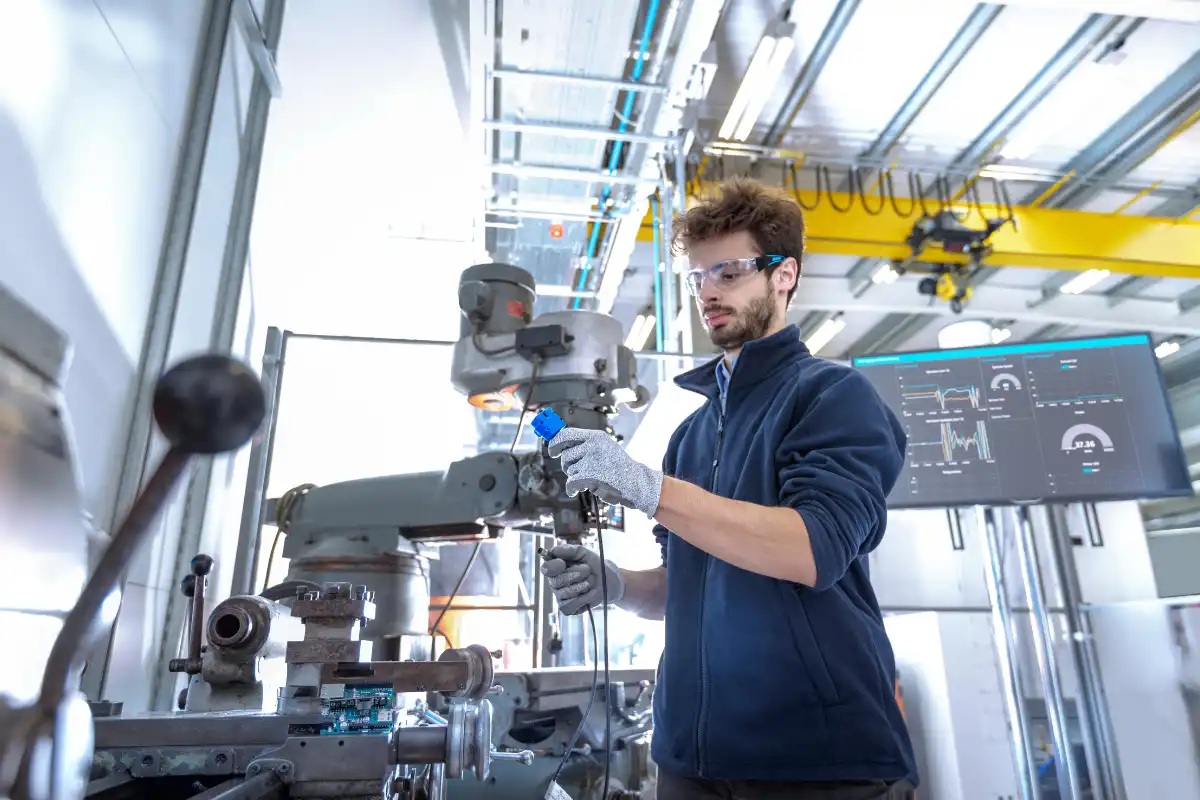
Every bit of apparatus tells a narrative. When a machine fails, it’s not simply an inconvenience — it’s a message.
However too usually, that message is ignored, misinterpreted, or misplaced in a sea of incomplete upkeep information. As an alternative of understanding why failures occur and stop them, upkeep groups are left scrambling to repair the problem and transfer on to the subsequent.
For giant enterprises managing complicated facility and asset portfolios, this reactive strategy is a expensive gamble. Unplanned downtime can disrupt operations, drive up restore prices, and shorten asset lifespan. But, many organizations nonetheless lack a scientific solution to seize, analyze, and be taught from tools failures.
That is the place failure codes are available in.
Let’s discover how failure codes work, why they’re important for enterprise upkeep administration, and the way they combine with trendy asset monitoring and facility administration options.
What are failure codes, and why do they matter?
Failure codes act as a common language for asset failures, enabling organizations to trace patterns, enhance preventive upkeep methods, and optimize useful resource allocation. They don’t simply inform upkeep groups what failed — they supply perception into why it occurred and stop it sooner or later.
If failure codes aren’t a part of your asset administration technique, you’re lacking a key instrument for decreasing downtime, bettering effectivity, and lengthening asset life
At their core, failure codes are standardized labels assigned to asset breakdowns, capturing important particulars concerning the concern. When an asset fails, a technician logs the failure right into a upkeep administration system, deciding on the suitable failure code that describes the issue. This might embrace:
- Mechanical failure (e.g., overheating, bearing failure, motor burnout)
- Electrical failure (e.g., quick circuits, voltage spikes, wiring degradation)
- Structural points (e.g., corrosion, cracks, misalignment)
- Software program/system malfunctions (e.g., sensor failure, connectivity loss)
These codes are extra than simply upkeep checkboxes — they function historic information that feed into preventive and predictive upkeep applications. When linked to an enterprise asset administration (EAM) or computerized upkeep administration system (CMMS), failure codes enable groups to establish developments, spot recurring points, and optimize asset inspection and servicing schedules.
For giant enterprises working a number of areas with 1000’s of property, failure codes are indispensable. They supply standardized failure monitoring throughout all websites, making certain that upkeep groups communicate the identical language and act on data-driven insights fairly than assumptions.
The excessive price of ignoring failure knowledge
With out failure codes, asset administration turns into a reactive cycle of breakdowns and rushed repairs. Organizations could expertise:
- Unplanned downtime that disrupts operations: When failure developments go untracked, groups can’t predict or stop breakdowns, resulting in sudden tools failures.
- Escalating restore prices: Emergency fixes and last-minute half replacements are considerably dearer than deliberate upkeep.
- Shortened asset lifespan: Repeated failures speed up put on and tear, resulting in untimely asset alternative.
- Compliance and security dangers: Tools failures can result in security hazards, regulatory violations, and legal responsibility issues if not correctly documented and addressed.
Take into account a big manufacturing facility that experiences frequent HVAC system failures. And not using a structured failure monitoring system, upkeep groups would possibly repeatedly repair particular person points with out recognizing an underlying sample — resembling frequent compressor failures as a consequence of poor airflow administration. By implementing failure codes and analyzing the historic knowledge, they may establish the foundation trigger, modify preventive upkeep schedules, and scale back expensive breakdowns.
This shift from reactive to proactive upkeep is simply attainable when organizations seize, analyze, and act on failure knowledge.
How failure codes combine with sensible upkeep methods
Trendy enterprise upkeep platforms have revolutionized the way in which organizations observe, handle, and forestall asset failures. These platforms combine failure codes immediately into asset checklists and inspection logs, making certain that each recorded failure turns into a part of an asset’s long-term historical past.
Capturing failure knowledge on the supply
When an asset malfunctions, a technician logs the failure into the system, deciding on a predefined failure code that categorizes the problem. This ensures that failure monitoring is constant throughout all areas, eliminating guesswork and subjective reporting.
Linking failures to preventive upkeep plans
With failure codes tied to asset historical past, organizations can establish developments — resembling which parts fail most frequently, which property require frequent repairs, and which areas expertise the best failure charges. This knowledge feeds into preventive upkeep schedules, permitting groups to service high-risk tools earlier than failure happens.
Enabling predictive upkeep with AI and IoT
When mixed with IoT sensors and AI-driven analytics, failure codes empower facility managers to combine them into their predictive upkeep methods. By analyzing failure developments in actual time, upkeep groups can anticipate when an asset is more likely to fail and take proactive steps — resembling changing worn-out parts earlier than a important breakdown.
For instance, a hospital facility supervisor utilizing an IoT-connected CMMS would possibly obtain an alert {that a} backup generator has logged a number of overheating failures up to now six months. As an alternative of ready for the generator to fail throughout an emergency, the system recommends an inspection, stopping a catastrophic failure throughout an influence outage.
This degree of data-driven decision-making is simply attainable when failure codes are used successfully.
Standardizing failure codes throughout giant enterprises
For giant organizations, one of many largest challenges in upkeep administration is standardization. With a number of services, tools varieties, and upkeep groups, making certain that everybody follows the identical reporting framework is crucial.
By implementing a centralized failure code system, enterprises can:
- Guarantee consistency throughout areas: A failure logged in a single facility means the identical factor in one other, permitting for enterprise-wide evaluation.
- Enhance technician effectivity: Upkeep groups can shortly reference previous failure knowledge, decreasing prognosis time and rising restore accuracy.
- Improve compliance and reporting: Regulatory audits change into simpler when organizations have structured upkeep information with clear failure histories.
A retail chain with lots of of shops, for instance, can use standardized failure codes to trace refrigeration unit malfunctions. If one retailer experiences compressor failures thrice extra continuously than others, facility managers can examine set up errors, environmental elements, or upkeep gaps — stopping a chain-wide concern.
The way forward for failure monitoring in enterprise upkeep
The function of failure codes in asset administration will solely develop as automation, IoT, and AI-driven upkeep platforms proceed to evolve. Enterprises that leverage failure knowledge to drive upkeep methods will see longer asset lifespans, fewer disruptions, and decrease operational prices.
For organizations nonetheless counting on guide upkeep logs or inconsistent monitoring strategies, the time to modernize is now. Integrating failure codes into a complicated facility and asset administration system isn’t nearly logging what went flawed — it’s about stopping failures earlier than they occur.
In case your group needs to maneuver past reactive upkeep, begin with failure codes. On the planet of asset administration, each failure tells a narrative — the true query is whether or not you’re listening.
Get in contact to learn how Eptura Asset and Archibus by Eptura can additional streamline your asset administration technique.