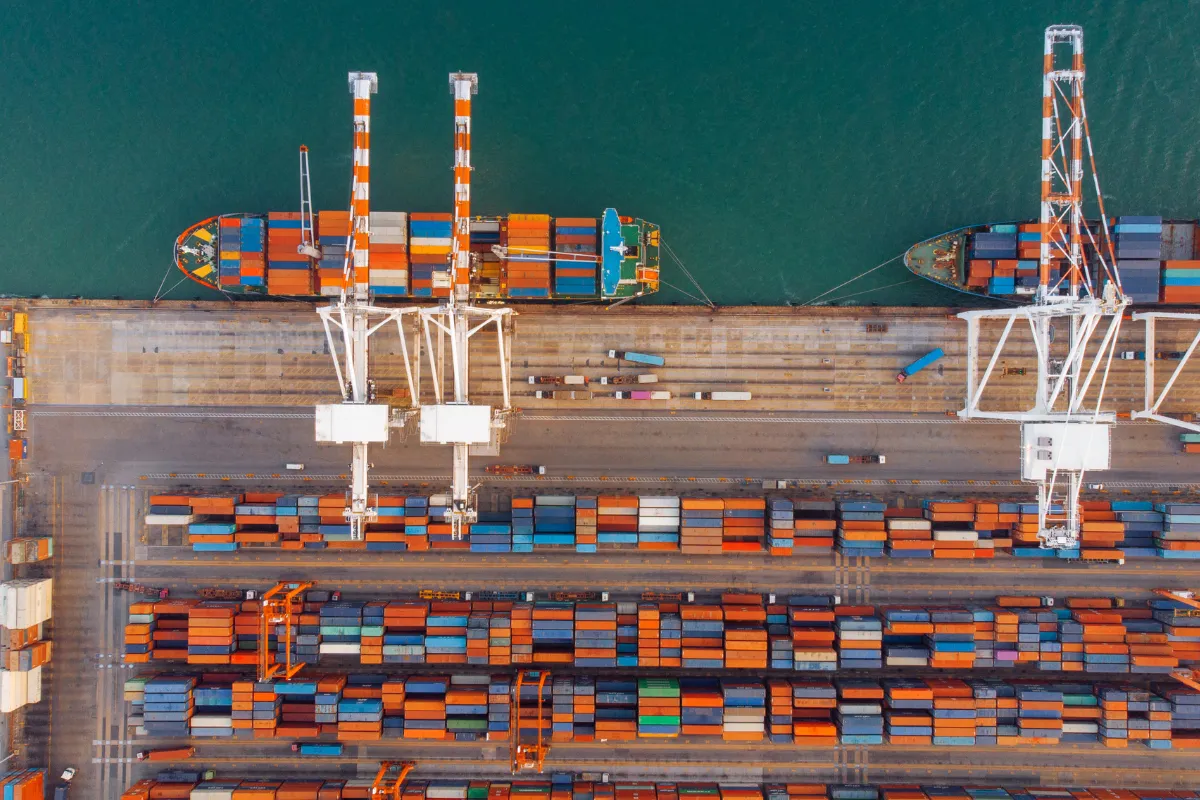
In right this moment’s world of interconnected economies. upkeep groups want strong stock administration that delivers dependable inventory ranges by correct demand forecasting and efficient price controls. By guaranteeing that the best elements can be found on the proper occasions, digital stock options assist facility and upkeep professionals keep operational effectivity.
What are the challenges of handbook stock monitoring for facility and upkeep administration?
Manually monitoring stock for upkeep and facility groups takes additional effort and time whereas nonetheless delivering disappointing outcomes. However that doesn’t imply each group will expertise the identical set of issues. All of it is determined by the particular circumstances, together with every part from business to current stock processes and insurance policies, explains Sammy Samperi, an enterprise account government at Eptura.
The widespread issues he hears about from firms embrace:
- General inefficiency: Manually monitoring stock is time consuming and labor intensive. It takes loads of time to depend, document, and replace stock ranges, which might be higher spent on different duties.
- Inconsistent knowledge: With no centralized system, completely different groups or areas would possibly keep their very own data, resulting in inconsistencies and discrepancies, making it tough to get an correct general image of stock ranges.
- Issue auditing: Tracing the historical past of stock actions throughout a number of handbook logs and spreadsheets takes loads of effort and time, making it laborious to make sure compliance with regulatory necessities.
- Decreased accountability: Guide methods make it more durable to trace who has accessed stock and when, resulting in points with theft, misuse, or misplacement of things.
- Elevated danger of stockouts: With out real-time visibility, it’s simple to overlook when stock ranges are working low, resulting in stockouts. What might have been a fast repair as a substitute turns into lengthy, costly unscheduled downtime.
Managing stock is a balancing act, so it’s necessary to not overcompensate when making an attempt to keep away from stockouts, explains Samperi.
“You recognize you could convey your fill up, however you don’t need to overstock. As a result of then you’ve cash tied up in stock that simply sits there depreciating, and also you’re not getting any worth from it.”
Upkeep stock challenges particular to bigger, enterprise-level firms
There are additionally stock points extra doubtless at bigger organizations, particularly these unfold out throughout a number of areas. For instance, handbook stock monitoring means missed larger missed alternatives. With out superior analytics and reporting, it’s tough to determine developments, optimize stock ranges, and make data-driven selections. So, a big manufacturing firm with a number of crops would possibly wrestle to find out the longevity and reliability of particular machine elements although they’ve knowledge units associated to elements and supplies. The issue is that not one of the units are related, and the shortage of visibility means missed insights.
One other problem is that handbook strategies don’t scale. As an organization expands, the complexity of handbook stock monitoring will increase exponentially, and it turns into more and more tough to handle bigger and extra various inventories. For instance, there could be a big manufacturing firm that’s increasing its manufacturing amenities to new areas. Every plant introduces a set of upkeep elements, similar to bearings, belts, and lubricants. As a result of the corporate can’t centralize and standardize stock administration processes, not solely can they not handle stock at anyone location, however additionally they can’t share stock throughout areas or get monetary savings by bulk purchases.
Points with stock and the worldwide provide chain
When inside processes for stock monitoring are unreliable, upkeep departments typically encounter extra points when making an attempt to answer fluctuations and disruptions in native and international provide chains. As a result of they lack dependable methods for inside monitoring, it’s inconceivable for them to effectively, successfully coordinate with suppliers.
When making an attempt to manage stock utilizing outdated strategies, the widespread challenges embrace:
- Demand forecasting inaccuracy: Predicting the precise demand for elements and provides will be tough, resulting in overstocking or stockouts. Overstocking ties up capital and will increase storage prices, whereas stockouts can result in downtime and elevated emergency orders.
- Lead time variability: The time it takes to obtain an order can differ considerably, making it tough to plan stock ranges. Lengthy or unpredictable lead occasions can lead to stockouts and elevated security inventory, which ties up capital.
- Seasonal fluctuations: Demand for sure elements and provides can differ considerably by season, making it tough to keep up optimum stock ranges, resulting in overstocking throughout low-demand intervals and stockouts throughout high-demand intervals.
Though there are lots of methods stock management for a upkeep group can go incorrect, there’s one dependable reply: A contemporary digital stock administration answer.
What are the advantages of digital monitoring for upkeep elements and provides?
Upkeep departments that leverage fashionable stock administration have the best elements, on the proper costs, and simply in time.
Decreased downtime
Figuring out precisely what elements a upkeep group has readily available is essential for minimizing tools downtime. When upkeep techs can shortly find and entry the mandatory elements, they will carry out repairs and upkeep duties extra effectively. Rapid entry to elements ensures that the group can convey tools again on-line quicker, decreasing the time that machines or methods are out of service. If a important piece of equipment breaks down, having the precise half readily available can imply the distinction between a fast restore and a chronic shutdown that pushes again manufacturing runes, risking reputational harm for the group.
Correct stock knowledge additionally helps preventive upkeep by guaranteeing that every one required elements can be found when scheduled upkeep is due, additional decreasing the probability of surprising downtime.
Value financial savings
By understanding precisely what elements are readily available, upkeep groups can keep away from overstocking, which ties up capital and will increase storage prices. Overstocking may also result in elements turning into out of date or broken, additional losing sources. However, correct stock knowledge helps in decreasing the necessity for emergency orders and expedited delivery, which are sometimes costlier. Optimized stock administration ensures that the best steadiness is struck between having sufficient elements to fulfill demand and avoiding pointless bills.
Improved effectivity
Correct stock knowledge streamlines workflows and improves general effectivity for upkeep groups. When groups know precisely what elements can be found, they will plan and execute duties extra successfully. They’ll shut out work orders quicker and allocate sources extra effectively.
For instance, if a upkeep process requires a particular half, the group can begin the job instantly with out ready for the half to be situated or ordered. Effectivity not solely quickens the upkeep course of but in addition permits groups to deal with extra duties, enhancing productiveness. And higher useful resource allocation ensures that the best elements can be found on the proper time, decreasing the probability of delays and bettering the general upkeep course of.
Improved compliance and security
In lots of industries, correct stock data are important for guaranteeing compliance with regulatory requirements and sustaining security. Figuring out precisely what elements can be found helps groups confirm that every one elements and supplies meet the mandatory regulatory necessities, decreasing the chance of non-compliance and related penalties.
For instance, in industries like healthcare or aviation, the place security is paramount, having the best elements readily available ensures that upkeep duties will be carried out to the best requirements. And correct stock knowledge helps security by guaranteeing that upkeep duties will be accomplished with out delays, decreasing the chance of accidents and accidents. So, if a safety-critical half is understood to be in inventory, the upkeep group can carry out the mandatory repairs instantly, guaranteeing that the tools stays secure to function.
Higher decision-making
Having a transparent and correct stock supplies a strong basis for making knowledgeable selections. Upkeep managers can use this knowledge to determine developments partially utilization, optimize stock ranges, and make strategic buying selections. For instance, if knowledge reveals a specific half is often wanted, the group can guarantee they at all times have ample inventory.
And groups can leverage historic knowledge and real-time efficiency metrics to foretell when elements will have to be changed. Predictive upkeep functionality permits for proactive planning, decreasing the probability of surprising failures and related prices. As an illustration, if the system predicts {that a} piece of kit is more likely to fail within the subsequent month, the group can order the required elements upfront, guaranteeing they’re readily available when wanted.
Higher provider relationships and provide chain administration
Correct stock knowledge may also result in higher relationships with suppliers. By inserting orders extra precisely and constantly, upkeep groups can negotiate higher phrases and construct stronger provider relationships. For instance, if a provider is aware of {that a} facility constantly orders the best variety of elements, they could provide higher pricing or extra favorable phrases. One other instance is when a big firm has visibility on its upkeep stock throughout a number of areas, empowering it to make bulk purchases that drive down prices.
And correct stock knowledge helps to raised coordinate with suppliers, probably decreasing lead occasions and guaranteeing well timed supply. If a upkeep group is aware of {that a} explicit half is working low, they will place an order nicely upfront, guaranteeing that the half arrives earlier than it’s wanted. A proactive strategy not solely improves the effectivity of the upkeep course of but in addition strengthens the connection with suppliers.
How can organizations leverage a contemporary upkeep administration platform to stock management?
A fashionable facility and upkeep administration answer can present the insights wanted to raised management stock by leveraging superior analytics and real-time knowledge integration. These options can analyze historic knowledge on elements and supplies utilization, upkeep schedules, and even predictive upkeep knowledge to forecast demand extra precisely.
For instance, a contemporary digital answer can combine knowledge from numerous sources, similar to upkeep logs, work orders, and tools efficiency metrics. The mixing permits the system to determine patterns and developments partially utilization, serving to to foretell when particular elements can be wanted. By connecting this knowledge to upkeep schedules, the system can routinely alter stock ranges to make sure that elements can be found when scheduled upkeep is due. The group can’t solely scale back the chance of stockouts but in addition decrease the necessity for extreme security inventory, optimizing stock ranges, and decreasing carrying prices.
And predictive upkeep capabilities inside these options can present much more granular insights. By utilizing machine studying algorithms, the upkeep division can use the system to foretell when tools is more likely to fail based mostly on real-time efficiency knowledge. An early warning system permits upkeep groups to proactively order and inventory the mandatory elements and supplies nicely upfront, stopping surprising downtime and decreasing the necessity for emergency orders. For instance, if the system predicts {that a} explicit piece of kit is more likely to fail within the subsequent month, it may routinely set off an order for the required elements, guaranteeing they’re readily available when wanted.
How can organizations efficiently implement a digital stock answer?
In accordance with Samperi, all of it begins with a profitable implementation supported by clear knowledge. So, he encourages firms to “actually spend time on this and get it proper.” In some instances, firms could need to use knowledge they have already got of their present stock system. As a substitute, he encourages firms to see the implementation course of as a possibility to start out with numbers they know they will belief, even when it takes extra time.
“And as soon as they do this, as soon as they spend that point, they’re going to routinely begin seeing that knowledge roll in and begin getting a few of their returns again in a short time.”